The saxophone stands as one of the most versatile and expressive instruments in modern music. From the smooth tones of jazz to the powerful sounds of rock and classical compositions, the saxophone’s distinctive voice has captivated audiences for nearly two centuries. But have you ever wondered what gives this remarkable instrument its unique sound and appearance? The materials used in saxophone construction play a crucial role in determining not just how the instrument looks, but how it sounds and performs.
In this comprehensive guide, we’ll explore the various materials used to craft saxophones, from traditional options to modern innovations. Understanding these materials can help musicians make informed decisions when selecting an instrument and provide fascinating insights for anyone interested in the science and craftsmanship behind musical instruments.
Check out our article over the best saxophone brands here.
Table of Contents
- 1 The Primary Material: Brass
- 2 The Finish: More Than Just Appearance
- 3 Key Components and Their Materials
- 4 Special Materials in High-End Saxophones
- 5 Modern Material Innovations
- 6 How Materials Affect Sound
- 7 Choosing the Right Material for Your Needs
- 8 Caring for Different Saxophone Materials
- 9 Conclusion
The Primary Material: Brass
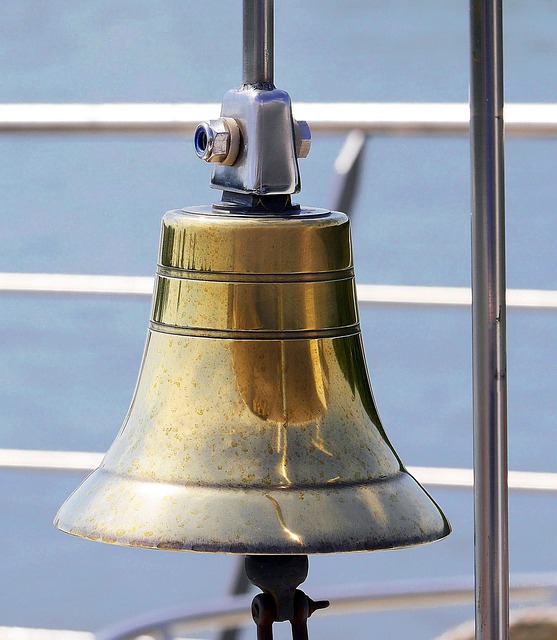
At its core, a saxophone is primarily constructed from brass, a metal alloy composed mainly of copper and zinc. This fundamental fact might surprise some people who assume from the golden appearance of many saxophones that they’re made of gold or another precious metal.
Brass is the material of choice for saxophone bodies for several compelling reasons:
Acoustic Properties
Brass offers excellent acoustic properties that contribute to the saxophone’s distinctive sound. It provides a perfect balance of rigidity and flexibility that allows the metal to vibrate in response to sound waves, enhancing the instrument’s resonance and tonal qualities. The density of brass helps create the warm, rich tone that saxophones are known for.
Durability and Workability
As a material, brass strikes an ideal balance between durability and workability. It’s strong enough to withstand the rigors of regular use while being malleable enough to be formed into the saxophone’s complex curved shape. This combination makes it possible to create the instrument’s intricate design with precision.
Types of Brass Used
Not all saxophones use identical brass compositions. Different manufacturers employ various brass alloys, each with slightly different ratios of copper to zinc and sometimes including other metals:
- Yellow brass (70% copper, 30% zinc) is the most common type used in saxophone construction. It provides a bright, projecting sound and is featured in many student and intermediate models.
- Gold brass (85% copper, 15% zinc) has a higher copper content that results in a warmer, darker tone. Many professional saxophones use this alloy for its rich sound characteristics.
- Red brass (90% copper, 10% zinc) contains the highest copper content of common saxophone brass alloys. It produces the warmest, darkest tone and is often found in high-end professional instruments.
The Yanagisawa WO Series saxophones exemplify the use of different brass alloys, offering models in various brass compositions to suit different tonal preferences.
The Finish: More Than Just Appearance
While the saxophone’s body is made of brass, what we see on the outside is typically a finish applied to the brass. These finishes serve both aesthetic and practical purposes.
Lacquer
Lacquer is the most common finish found on saxophones. It’s a clear or colored coating that protects the brass from tarnishing while allowing the metal to vibrate naturally. Different types of lacquer include:
- Clear lacquer allows the natural brass color to show through
- Gold lacquer adds a warm, golden appearance
- Colored lacquers (black, silver, etc.) create unique visual effects
The Yamaha YAS-280 Alto Saxophone features a clear lacquer finish that showcases the beautiful brass beneath while providing protection against tarnishing.
Silver Plating
Some saxophones receive a plating of actual silver over the brass body. Silver plating offers:
- A distinctive bright, silvery appearance
- Slightly different acoustic properties than lacquered instruments
- Greater durability in some environments
The Selmer Paris Series III Alto Saxophone is available with silver plating, offering both visual elegance and unique tonal characteristics.
Nickel Plating
Nickel plating provides a silvery appearance similar to silver but with different properties:
- More resistant to corrosion than silver
- Typically more affordable than silver plating
- Slightly brighter acoustic response
Raw Brass
Some high-end and vintage-inspired saxophones come with no finish at all, leaving the raw brass exposed. This approach:
- Allows maximum vibration of the metal
- Develops a natural patina over time
- Requires more maintenance to prevent tarnishing
The P. Mauriat PMXT-66R Tenor Saxophone offers a “Dark Vintage” unlacquered finish that many professional players prize for its resonant qualities and distinctive appearance.
Key Components and Their Materials
While the body may be brass, a saxophone consists of many parts made from various materials, each chosen for specific properties.
Keypads and Resonators
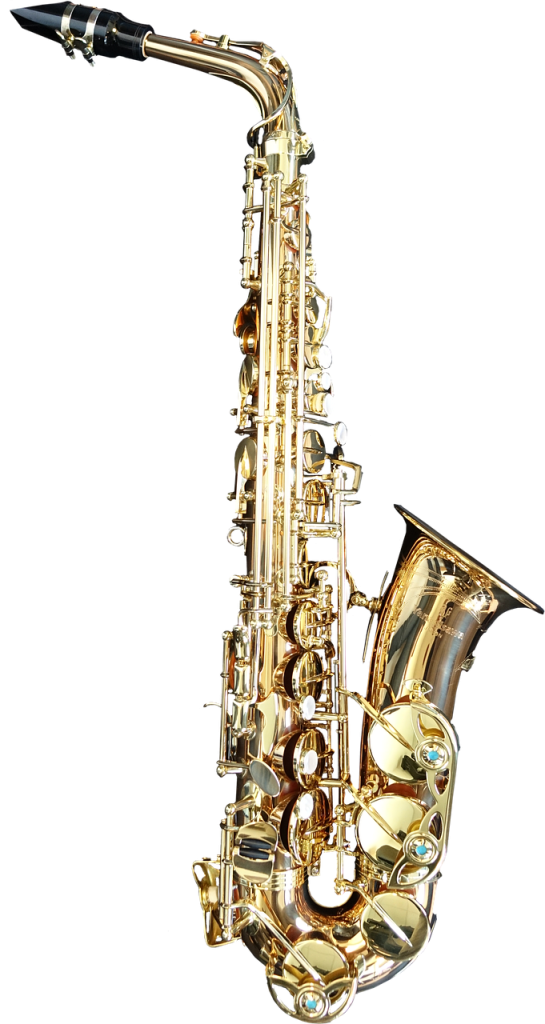
The keypads that seal the tone holes are typically made of:
- Leather (usually fish skin or goatskin) for the pad itself
- Felt for cushioning between the pad and its cup
- Cardboard or synthetic material for backing
The resonators (the metal discs in the center of pads) can be:
- Metal (brass, nickel, or plastic-covered metal)
- Plastic
The choice of pad and resonator materials significantly affects playability, maintenance requirements, and even tone.
Key Mechanisms
The complex key system that makes the saxophone playable consists of:
- Brass for the key arms and levers
- Steel for springs and rods
- Cork, felt, or synthetic materials for key buffers and silencers
These materials must withstand constant use while maintaining precise adjustment.
The Jean Paul USA AS-400 Alto Saxophone demonstrates quality key mechanisms designed for durability and smooth action, essential for students and advancing players alike.
Mouthpiece
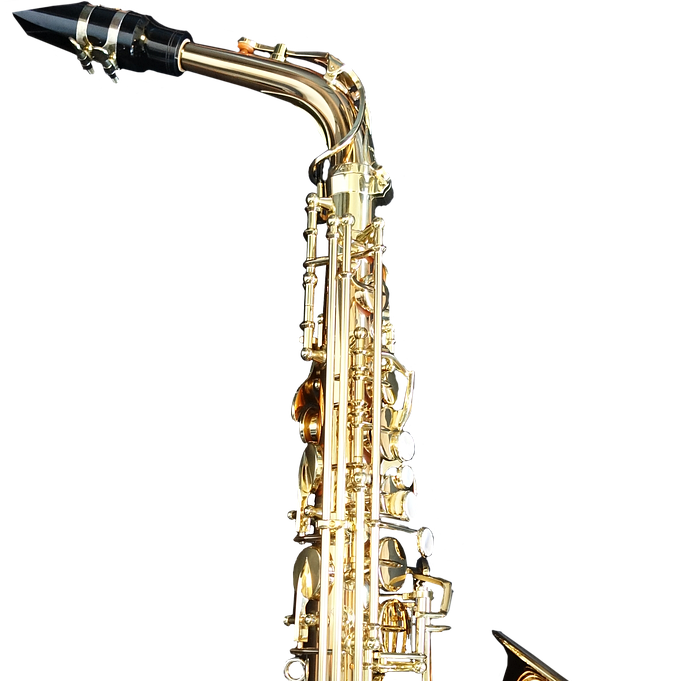
Perhaps no component affects the saxophone’s sound more than the mouthpiece, which is typically made from:
- Hard rubber (ebonite): The traditional material, known for its warm sound
- Metal: Provides a brighter, more projecting tone
- Plastic: Common in student models for durability and consistency
- Wood: Rare, but used for specific tonal qualities
- Glass or crystal: Used by some boutique manufacturers for unique acoustic properties
The mouthpiece material dramatically influences the instrument’s sound, with each material offering distinct tonal characteristics.
Ligature
The ligature, which holds the reed to the mouthpiece, can be made from:
- Metal (brass, nickel-plated brass, or silver-plated brass)
- Leather
- Synthetic materials
- String (in some traditional designs)
Like other components, the ligature’s material and design contribute to the saxophone’s overall sound and response.
Reed
The reed, which vibrates to create sound, is typically made from:
- Cane (Arundo donax): The traditional and most common material
- Synthetic materials: Offering greater consistency and durability
While not part of the saxophone itself, the reed is crucial to sound production and is considered an essential component of the instrument system.
Special Materials in High-End Saxophones
Premium saxophones sometimes incorporate special materials for enhanced performance or aesthetic appeal.
Bronze
Some high-end saxophones use bronze (an alloy of copper and tin) instead of or in addition to brass. Bronze offers:
- A darker, more complex tonal palette
- Different resonance characteristics
- Distinctive appearance
Sterling Silver
Beyond mere silver plating, some luxury saxophones feature components made of solid sterling silver:
- Neck (the curved tube connecting the mouthpiece to the body)
- Bell (the flared end of the instrument)
- Key touches (the parts players actually touch)
The Yanagisawa S-WO37 Soprano Saxophone features a solid silver neck that contributes to its exceptional tonal qualities and response.
Gold Plating
For the ultimate in luxury and distinctive appearance, some saxophones feature actual gold plating:
- Typically 24K gold over a brass body
- Often reserved for special edition instruments
- Provides both visual appeal and subtle tonal differences
The Selmer Paris Reference 54 Tenor Saxophone is available with gold plating on specific models, creating both visual and acoustic luxury.
Modern Material Innovations
Saxophone makers continue to experiment with new materials and manufacturing techniques.
Composite Materials
Some manufacturers have developed saxophones using modern composite materials:
- Carbon fiber components for lightweight strength
- Synthetic resins for consistent production
- Hybrid designs combining traditional and modern materials
These innovations aim to address specific challenges in traditional saxophone design, such as weight, durability, and consistency.
3D Printing
Cutting-edge manufacturing technologies are beginning to influence saxophone production:
- Prototyping new designs
- Creating components with complex internal structures
- Producing custom parts for unique player requirements
While still emerging, these technologies may significantly impact how saxophones are made in the future.
How Materials Affect Sound
The materials used in saxophone construction profoundly influence the instrument’s sound characteristics.
Density and Resonance
The density of metals used in saxophone construction affects how the instrument resonates:
- Higher density metals (like those with more copper) tend to produce darker, richer tones
- Lower density alloys often create brighter, more projecting sounds
Thickness and Weight
The thickness of the brass used in the saxophone body impacts both sound and playability:
- Thicker materials generally produce fuller sounds with more overtones
- Thinner materials can increase responsiveness and reduce weight
Finish Impact
The type of finish applied to a saxophone affects its sound in subtle but noticeable ways:
- Lacquer slightly dampens vibrations compared to raw brass
- Silver plating offers different vibration characteristics than lacquer
- The aging of finishes over time can change an instrument’s sound
Choosing the Right Material for Your Needs
With all these material options, how do you choose what’s right for you?
Consider Your Playing Style
Different materials complement different musical genres and playing styles:
- Jazz performers might prefer materials that offer flexibility and warmth
- Classical saxophonists often seek precision and consistency
- Rock and pop players may prioritize projection and durability
Testing and Comparison
When possible, try instruments with different materials to discover your preferences:
- Compare lacquered versus silver-plated instruments
- Try mouthpieces made from different materials
- Consider how different brass alloys affect your personal sound
Budget Considerations
Material choices significantly impact instrument pricing:
- Student instruments typically use standard materials focused on durability
- Professional models offer material options that enhance specific tonal qualities
- Luxury instruments may incorporate precious metals and special alloys
Caring for Different Saxophone Materials
Different materials require specific maintenance approaches to ensure longevity.
Brass and Finishes
- Lacquered brass requires gentle cleaning with non-abrasive cloths
- Silver plating needs special silver cleaning products to prevent tarnishing
- Raw brass develops a patina that some players prize but requires regular maintenance
Pads and Corks
- Leather pads need protection from excessive moisture
- Cork components require occasional replacement and light lubrication
- Synthetic alternatives may offer greater durability but different feel
Conclusion
The saxophone’s unique voice in music comes not just from its design but from the carefully selected materials used in its construction. From the brass body to the specialized components, each material choice represents a balance between tradition, innovation, sound quality, and practicality.
Whether you’re a player seeking the perfect instrument, a student learning about musical acoustics, or simply curious about how saxophones are made, understanding these materials provides valuable insight into what makes this remarkable instrument so special.
The next time you hear a saxophone’s evocative sound, you’ll appreciate that it’s not just the player’s skill you’re hearing, but the voice of carefully chosen materials working in harmony to create one of music’s most expressive voices.